The Role of Tested Tool Steel in Enhancing Manufacturing Efficiency
In today’s competitive manufacturing environment, efficiency is paramount. The role of tested steel is becoming more relevant in today high tech and quality conscious customer.
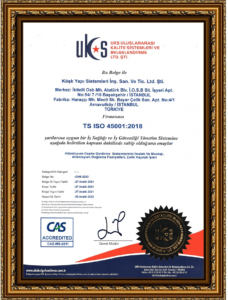
Companies continually seek ways to improve productivity while minimizing downtime and costs. One critical component in this pursuit is the use of tested tool steel, which plays a significant role in enhancing manufacturing processes. Many opt for a non-certified non-tested steel as the costs are lower, however this can impact your business and reliability. Studies have shown that tested tool steels work out cheaper in the long run as the rejection and breakdown rates become far lower.
This article delves into how tested tool steel contributes to improved productivity, explores real-world case studies, and provides industry examples of its impact on manufacturing efficiency.
The Importance of Tested Tool Steel in Manufacturing
Tool steel is a specific type of carbon alloy steel that is well-suited for making tools due to its hardness, resistance to abrasion, and ability to retain shape at elevated temperatures. Tested tool steel refers to grades that have undergone rigorous testing to ensure they meet the high standards required for manufacturing applications. These materials are essential in creating tools that are not only durable but also highly efficient in their performance.
How Tested Tool Steel Enhances Manufacturing Efficiency
- Improved Tool Longevity:
- Durability and Wear Resistance: One of the primary benefits of using tested tool steel is its superior durability. This material is engineered to withstand the intense conditions of manufacturing processes, such as high heat, pressure, and friction. Tools made from high-quality, tested tool steel can last significantly longer than those made from lower-grade materials, reducing the frequency of replacements and, consequently, downtime.
- Reduced Tool Wear: The wear-resistant properties of tool steel mean that tools maintain their cutting edges or mold shapes for extended periods, ensuring consistent performance and reducing the need for frequent retooling.
- Consistency and Precision:
- Maintaining Tolerances: In precision manufacturing, maintaining tight tolerances is critical. Tested tool steel provides the consistency needed to ensure that each manufactured part meets exact specifications. This consistency minimizes the risk of defects, leading to fewer rejected parts and less material waste.
- High Temperature Stability: Certain manufacturing processes involve high temperatures that can cause some materials to soften or deform. Tool steels, particularly those designed for hot work, retain their properties at elevated temperatures, ensuring that tools remain effective and precise throughout the production cycle.
- Increased Productivity:
- Faster Machining Speeds: Tools made from high-speed steel (HSS) or carbide-tipped steel can operate at higher speeds, reducing cycle times and increasing overall production rates. This acceleration in machining speeds directly translates to higher throughput in manufacturing environments.
- Enhanced Cutting Performance: The superior cutting capabilities of tested tool steel enable faster material removal rates, contributing to shorter production times and increased efficiency.
Case Studies and Industry Examples
Case Study 1: Automotive Manufacturing
An automotive parts manufacturer faced frequent downtime due to tool wear in their stamping processes. By switching to a high-performance, tested tool steel, the company extended the lifespan of their stamping tools by 40%. This change reduced downtime by 25%, allowing the manufacturer to increase production capacity and meet growing demand without additional investments in new equipment.
Case Study 2: Injection Molding
A plastic component manufacturer struggled with inconsistent mold performance, leading to defects and high scrap rates. By adopting a tested tool steel with superior thermal conductivity and wear resistance, the company achieved more consistent mold temperatures and reduced cycle times. This resulted in a 15% increase in productivity and a 30% reduction in material waste.
Industry Example: Aerospace Manufacturing
In the aerospace industry, where precision and reliability are critical, tool steel is used extensively in the machining of turbine blades and other components. Tested tool steels, such as those with cobalt or vanadium additives, are preferred due to their ability to maintain sharpness and resist wear under extreme conditions. The use of these materials has enabled aerospace manufacturers to produce components with high precision and minimal downtime, contributing to the overall efficiency of production lines.
Conclusion
The strategic use of tested tool steel in manufacturing offers significant advantages in terms of efficiency, productivity, and cost-effectiveness. By choosing high-quality, tested materials, manufacturers can reduce downtime, improve tool longevity, and enhance the precision of their processes. The impact of these improvements is evident across various industries, where the use of tool steel has led to tangible gains in production capacity and product quality.
Click here to know more about how Soni Steels maintains quality standards